When your packaging equipment breaks down during high-volume periods — like peak season or a major product launch — it's more than just a headache. It leads to costly production delays, missed deadlines, and frustrated warehouse teams. While many operations managers recognize the value of preventative maintenance, few have a packaging maintenance program that’s proactive, repeatable, and tied to real results.
Preventative maintenance shouldn’t be guesswork or just another box to check. It should be a core operations strategy that protects equipment uptime, reduces repair costs, and maximizes throughput.
1. Identify Your Most Critical Packaging Equipment
Start by determining which machines are essential to your operation and would cause the biggest disruption if they went down. These might include:
- Labeling machines
- Stretch wrap machines
- Strapping machines
- Case sealers
- Shrink wrap tunnels
- Carton erectors
For each machine, document:
- Its function in your packaging workflow
- Average daily or weekly runtime
- The downstream impact if it stops working (e.g., delays in outbound shipments or warehouse bottlenecks)
This is the first step in building a smart packaging equipment maintenance plan.
2. Combine OEM Guidelines with Real-World Data
Every piece of packaging equipment comes with a manufacturer’s maintenance guide, but these are general suggestions. Your actual usage — how often and how hard you run your machines — is even more important.
Track:
- Part replacements (e.g., belts, blades, heat elements)
- Unplanned repairs
- Hours of operation between service needs
- Operator feedback and error reports
This data helps you predict future issues and build a custom preventative maintenance schedule based on real performance — not just general recommendations.
3. Train Your Warehouse Staff for Daily Visual Checks
Your team is your first line of defense. Teaching them how to perform quick daily inspections can prevent minor issues from becoming major failures. Basic checks should include:
- Are belts tight and free from cracks?
- Are sensors clean and aligned properly?
- Are cutters, knives, or blades sharp and intact?
- Are bearings and gears moving smoothly?
- Are there any strange sounds, smells, or warning lights?
These 5-minute inspections add up. Training your team means fewer surprises and less downtime.
4. Build a Digital Preventative Maintenance Calendar
A simple, recurring calendar can keep everyone on the same page — whether you’re managing one machine or fifty. Your maintenance schedule should include:
- Monthly: Lubrication of moving parts, minor adjustments, filter replacements
- Quarterly: Sensor calibration, belt inspections, software updates
- Annually: Deep cleaning, wear-and-tear part replacements, safety tests
Keep the calendar digital so you can assign tasks, track completions, and adjust based on results. Whether you’re using a warehouse management system (WMS) or a simple spreadsheet, consistency is key.
5. Log Every Maintenance Activity
Every touchpoint matters — from a simple cleaning to a full motor replacement. Logging helps you:
- Spot recurring issues
- Justify upgrades to newer, more efficient machines
- Prove the value of your maintenance program
- Track vendor or technician performance
Use a centralized maintenance log or dashboard to keep detailed records. Over time, this becomes a valuable tool for operations forecasting and capital planning.
Why Preventative Maintenance Should Be Part of Your Packaging Strategy
Preventative maintenance for packaging equipment isn’t optional — it’s operational insurance. A clear, consistent plan helps you:
- Reduce unplanned downtime
- Extend the lifespan of packaging machinery
- Avoid last-minute repairs and rush-order part costs
- Keep your fulfillment promises during peak season
- Maintain productivity and cash flow
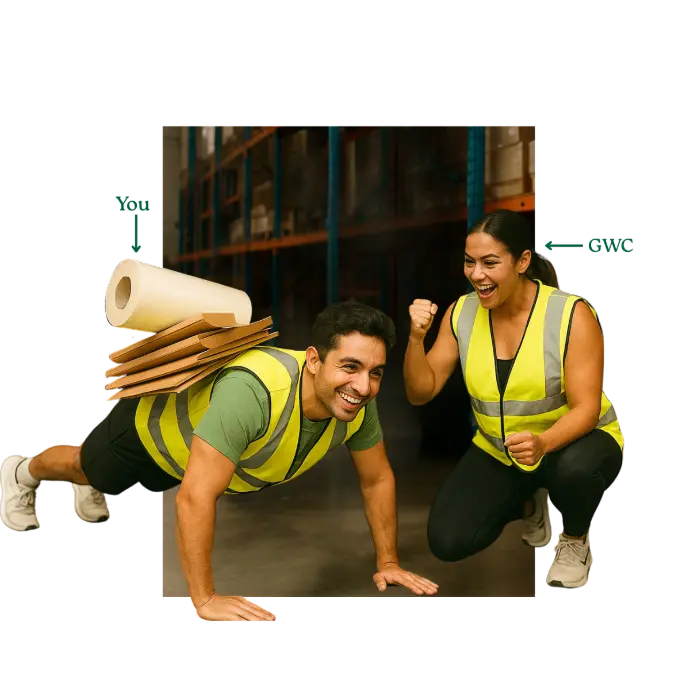
We’ll Help You Strengthen your packaging line from the inside out.
✅Catch Issues Early
✅Extend Equipment Lifespan
✅Protect Your Bottom Line—So When Peak Season Hits, Your Operations Don’t Skip a Beat.